FAQ
A: The Hat section is a much more rigid design than the Channel section:
1.) A higher moment of inertia and section modulus are achieved with less overall height.
2.) The bottom flanges increase the ability of the beam section to resist buckling when compared with a plain channel section.
3.) The beam is extremely rigid when it is subjected to eccentric loading from the broadside direction. The fact that the beam is bolted at the top and at the two bottom flanges creates an extremely rigid member. The DESIGNCO three place bolting method is a much more desirable and practical method when compared to channels which are only bolted at the top.
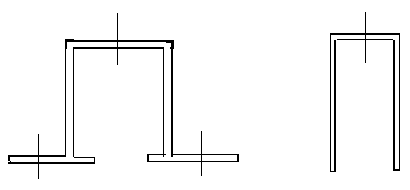
A: In order to have a raised access floor system stay on the 2' module which is now an almost universal standard in clean rooms, it is an absolute requirement that panels be specified and manufactured to less than the 24" module. Here are the reasons why:
1.) If the majority of the panels are oversize it is an impossibility to stay on a 24" module. No understructure system can compress the panels or shrink them.
2.) There must be clearance between the panels after installation for easy removal and reinstallation of the panel and for complete panel interchangeability.
3.) Panels as any other manufactured product require a manufacturing tolerance. Too stringent a tolerance just increases the cost of production to no real benefit for anyone. We recommend panels to be specified to range in size from 23.985" to 23.970" with finish applied. Panels produced to these dimensions will install easily, be easy to remove and will be interchangeable. Panels produced to these dimensions will work even when they are slightly parallelogram in configuration, which is another manufacturing reality.
4.) DESIGNCO punches all of the holes for the bolts and pins in the beams at one time using specially designed tooling to ensure complete repeatability of dimensions from one beam to the next. Our beams are maintained in a 67 degree to 71 degree environment which closely matches cleanroom temperature. This insures a minimum of change in dimensions due to temperature variations considering the coefficient of expansion of aluminum.
5.) DESIGNCO has built into their understructure system an adjustable mini-pedestal (Patent applied for) that is part of the 7"X7" and 6.5"X6.5" joining plates. This mini-pedestal can move a total distance of 1.983" or .969" in any direction from center, to accommodate and fit to any panel dimension that might occur.
A: The stainless steel pins accomplish the following:
1.) Speeds up the installation.
2.) Maintains the 4' or 6' dimension between beams and H.D. pedestals.
3.) Insures squareness of the system.
A: We started using pins at all of the joining plates and at the center of the cross beams but discovered that it is only necessary to use the pins at the 4' intersection and at the 6' intersections.
A: Aluminum is the most practical and acceptable material for clean room use, as is stainless steel. DESIGNCO furnishes aluminum in Mill Finish or Baked on Powder Coat, both conductive or non-conductive.
A: Yes. The DESIGNCO 4'X4' or 6'X6' system can be manufactured in steel (powder coated) or stainless steel if desired. Aluminum, stainless steel, or powder coated carbon steel may be mixed in the same system if desired. DESIGNCO recommends aluminum as the most satisfactory because of its universal acceptability for cleanroom use. It's lighter weight for lower shipping costs, ease of installation, and ease of field modification when required.
A: Not so. All of the beams are manufactured and shipped with stainless steel PEM nuts installed on the inside of the hat section beams. It is only necessary to screw in the top bolts.
A: Mainly because of the ability of the hat section to resist twisting and buckling better than the channel section plus we can bolt in three places instead of just one place. The hat section also develops a higher "Moment of Inertia" than does a channel section of the same height.
A: These flanges are for the purpose of mounting process piping hangers. These hangers are made by DESIGNCO for the specific size piping.
A: Yes! DESIGNCO's understructure will work with any available panel, aluminum, or steel. The panel manufacturer normally supplies his standard pedestal head. When the standard pedestal head requires upgrading because of higher than normal lateral or vertical loads, DESIGNCO can manufacture a pedestal head to suit.
A: All DESIGNCO pedestals are designed to act as cantilevered beams. There is no necessity for diagonal bracing which only wastes valuable under floor space and makes it more difficult for other trades to work around.
A: The diagonal beam system in a 4'X'4 system interferes with underside access to half of the panels on the job. With the 6'X6' system it is even worse. In a 6'X6' cell 5 of the 9 panels have the same problem. The 6'X6' diagonal beam system does not truly qualify as a 6'X6' system as it is necessary to add a prop pedestal in the center of the 6' diagonal beam.
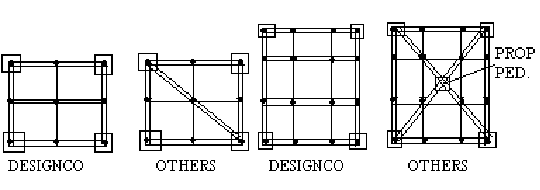
This is one of the major benefits of the DESIGNCO system. Every panel on a DESIGNCO job has clear access to the underside!
A: DESIGNCO approaches each job on an individual basis. The understructure beams, H.D. pedestals and anchoring to the concrete are all designed, engineered, and calculated to meet the specific job requirements. Engineering calculations furnished A.R.O. -State Certified Structural engineer stamped engineering calculations furnished at no charge on the larger jobs. DESIGNCO specializes in doing the more difficult jobs as are required in UBC zones 3 and 4. Design, engineering, calculations, and manufacturing are all done in the house.
A: The reason is the basic cost of steel is less than aluminum. Manufacturing and installation is faster with aluminum because of its lesser weight. However, aluminum is 1/3 the weight of steel and shipping costs are less.
Example: A 6' Module Steel Beam is about 97 lb.., vs. an aluminum unit of about 35 lb.. A 97 lb.. Beam requires two work men to handle etc. Any modification for tool fit up becomes very difficult and slow with the steel, when compared to the modification of aluminum understructure.
A: The DESIGNCO 4'X4' System has all of the beams placed perpendicular to one another. There are no beams placed at a 45 degree angle which are difficult to cut and fit to. All cuts with the DESIGNCO System are Square Cuts.
In some cases main beams may be made purposely longer than the 4' or 6' module and cantilevered with no support required at the end.
On longer beam extensions the beam can be braced back to the H.D. Pedestal at the base, in order to clear process piping, equipment, etc. that might be in the way. Much time is saved with the DESIGNCO System at tool fit up time, especially when compared to competitive steel systems and systems with 45 degree beams.
